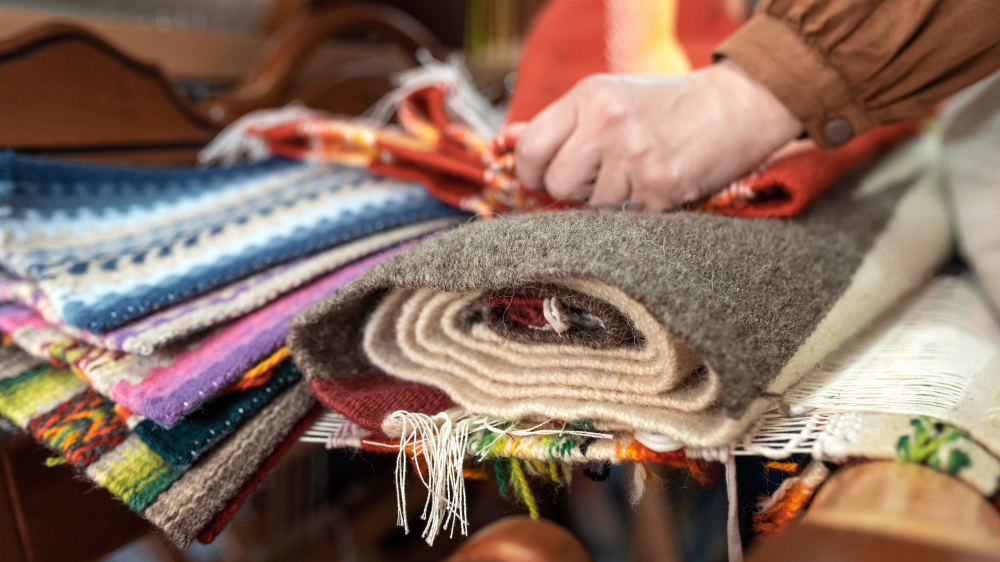
Woven garments are always prevalent when it comes to breathable summer clothing. With fashion trends constantly evolving, woven fabric manufacturing has become a thriving business, requiring an organised and efficient approach. If you are involved in the garment industry, you understand how crucial high-quality fabrics are in the competitive global market.
Producing the perfect fabric involves multiple steps, each critical to achieving the desired result. This blog outlines five essential steps you should consider when processing fabrics, helping you ensure successful woven fabric production.
Table of Contents
What is Woven Fabric?
Woven fabric is a textile created by interlacing two sets of threads—warp and weft—at right angles on a loom. This intricate process results in a versatile material that can vary in texture, weight, and durability, making it suitable for a wide range of applications, from clothing to home furnishings.
Historically, woven fabrics have played a vital role in human civilisation, dating back thousands of years when ancient cultures used primitive looms to create textiles for clothing and ceremonial purposes. Over time, the craft of weaving evolved, influencing trade and cultural exchanges across regions.
In modern textile production, woven fabrics remain significant due to their strength and versatility, as they are extensively used in fashion, upholstery, and industrial applications, reflecting advancements in technology and sustainable practices that continue to shape the industry today.
5 Essential Steps for Woven Fabric Manufacturing
In any garment sourcing company in Bangladesh, the apparel manufacturing process is a critical factor in delivering top-quality woven fabrics on time. A well-managed process leads to satisfied clients, while a poorly organised one can result in delays and subpar products. Whether you are an established garment manufacturer or new to the industry, this guide will help you better understand the steps involved in woven fabric production.
1. Yarn Winding
The first step in the woven fabric manufacturing pacrocess is yarn winding. Here, yarn is transferred from large cones into smaller packages known as bobbins. This stage is crucial because it determines the yarn’s quality before moving on to the subsequent phases. Yarn selection is based on the specific type of woven fabric being produced. Before winding, the yarn is inspected for any defects. The winding machine operates at a steady speed to ensure even winding without damaging the yarn.
2. Warping to Create Fabric Sheets
Warping involves organising yarns systematically to form sheets of fabric. It begins with creating, where the yarn cones are placed on racks. A protective coating is sometimes applied to enhance weaving performance. During the warping process, yarns are drawn from the creel and wound onto a large cylinder called the warping beam. This warp sheet is inspected for defects before moving forward.
3. Sizing the Threads
At this stage, the yarns are divided into single and double threads. To make the fabric more durable, the threads must maintain uniform quality. Single threads, which are delicate, are treated with sizing agents to strengthen the fibres. After drying, the threads are separated to prevent tangling during weaving.
4. Weaving into Patterns
The weaving process begins by creating a warp, where two or more threads are twisted to form the foundation of the fabric. Garment manufacturers typically use two sets of interwoven yarns. The most common weaving patterns are plain, twill, and satin. Modern weaving is done using electric looms, which complete the process efficiently. This phase is the most critical in woven fabric manufacturing and is carried out with precision in a controlled environment.
5. Finishing and Drying
The final stage involves several steps that prepare the fabric for its final form. These steps include steaming, washing, and heat setting. First, the fabric is dyed using colourants and chemicals and then steamed to ensure the dye penetrates appropriately. Excess dye and impurities are removed through washing. The fabric then undergoes dry finishing and brushing to soften its surface. Finally, the fabric is calendered to give it a smooth, shiny finish.
Moving Forward
Now that you are familiar with the five steps of woven fabric manufacturing, it’s time to apply this knowledge to your sourcing business. As an apparel-buying house company in Bangladesh, following these steps carefully will help you produce high-quality woven fabrics that meet client expectations and stand out in the market. By streamlining your production process, you can offer premium woven fabrics and ensensure timely delivery for your clients.